Visite | Zéfal : Made in France jusqu’au bout des pompes
Par Olivier Béart -
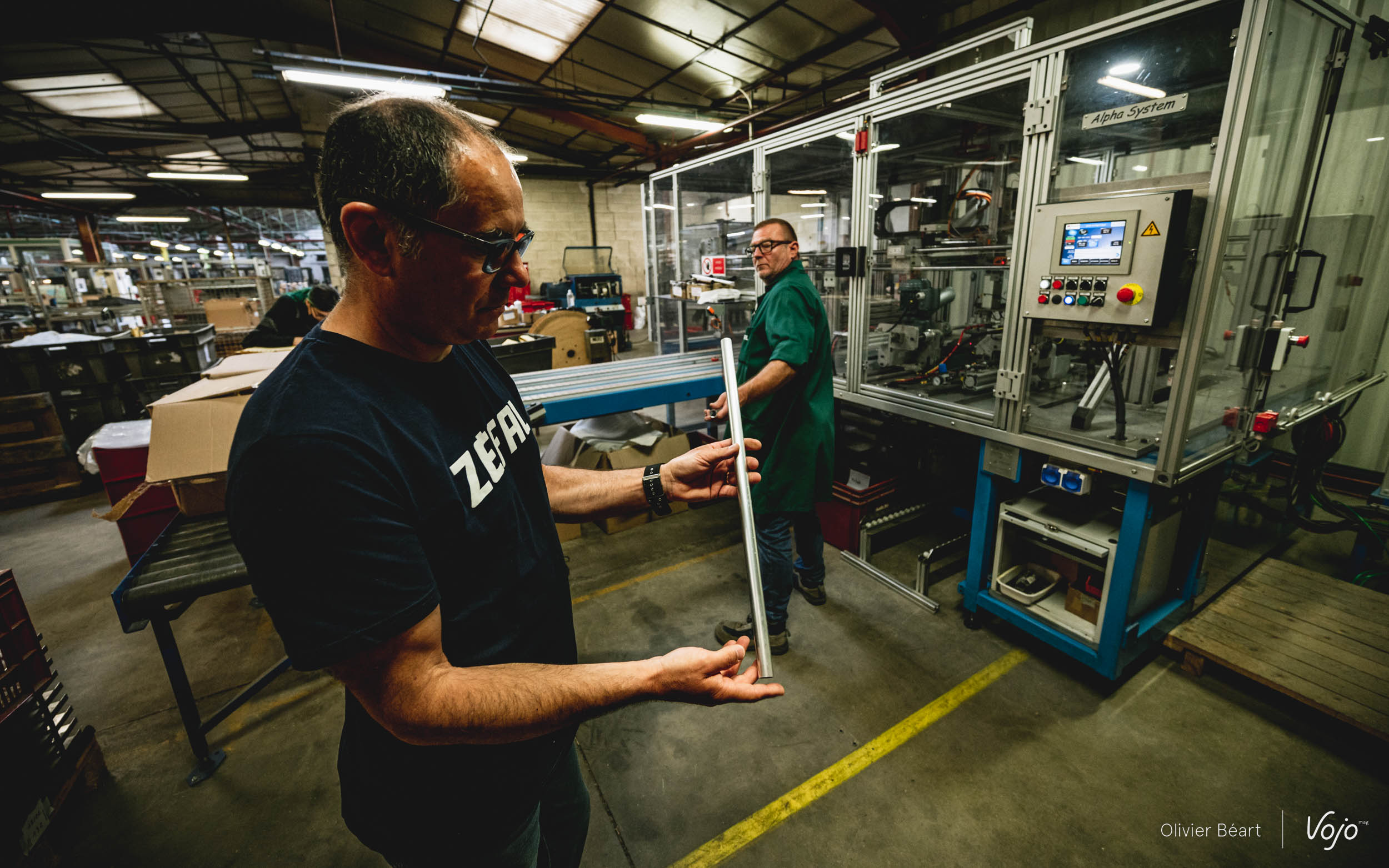
Vous connaissez certainement le nom de Zéfal, mais savez-vous que l’entreprise fabrique toujours la quasi totalité de ses produits en France, dans le Loiret ? Aluminium, acier, plastique : tout est travaillé ici jusqu’au dernier petit joint ou petit bouchon pour réaliser des pompes, bidons, porte-bidons et bien d’autres accessoires vélo indispensables. Vojo est parti à la découverte de cette marque qui a mis à profit sa riche histoire pour s’ancrer dans le présent.
La conception de pompes et d’accessoires de gonflage est venue tout naturellement suite à cela, mais le catalogue a toujours été très diversifié avec des sonnettes (qu’on appelait « timbres » à l’époque) ou encore les fameux cale-pieds « Christophe » dont la marque a acquis les droits de production au coureur qui les avait inventés. Ils sont d’ailleurs toujours produits aujourd’hui comme vous le verrez plus loin lors de notre visite !
Quant au site de Jargeau, au bord de la Loire, que nous avons visité et qui est toujours aujourd’hui le siège de Zéfal, il s’agit d’une ancienne féculerie qui a été acquise par la famille Brunet en 1936. A ses plus grandes périodes d’activité, l’usine a accueilli jusqu’à 300 personnes. Aujourd’hui, Zéfal tourne autour de 100 personnes et ce chiffre est en augmentation régulière.
Après une période plus compliquée il y a une quinzaine d’années, l’entreprise a été fameusement modernisée par Aurélien et Mathieu Brunet, qui ont pris la suite de leur père après avoir fait leurs armes dans d’autres domaines de l’industrie. Ils posent ici en compagnie de Vincent Cabanel, le responsable presse.
Les deux frères sont la 5e génération de Brunet à la tête de la manufacture ! Ensemble, les deux frères ont réussi à impulser une nouvelle dynamique à l’entreprise, tout en continuant à miser sur son riche passé et sur son savoir-faire Made in France encore bien vivace.
Cette rencontre entre passé et présent se remarque quasiment à chaque étape de notre visite. Dès le hall d’entrée, les anciennes affiches cyclistes (dont le père d’Aurélien et Mathieu était un grand collectionneur) côtoient les derniers produits de la marque.
Nous commençons ensuite notre visite des ateliers « par la fin », en compagnie du responsable technique Franck Palis. La disposition de l’usine est ainsi faite que nous démarrons par l’emballage et l’assemblage final d’accessoires pour vélo urbain, dont les garde-boue et les rétroviseurs qui sont aujourd’hui un des best-sellers de Zéfal.
Ce simple rétroviseur est bien plus complexe à fabriquer qu’il n’y paraît, notamment au niveau du miroir plastique incassable qui nécessite énormément de soin pour être bien réfléchissant. « Depuis la crise sanitaire les ventes de ce type de produit ont explosé. Même avant il y avait déjà une hausse de la demande, et c’est un bon baromètre de l’augmentation de l’usage du vélo urbain », nous explique Franck.
Au milieu de cette chaîne d’assemblage largement féminine, il ajoute non sans une certaine fierté : « En maîtrisant tout le processus en interne, nous avons non seulement réussi à tirer notre épingle du jeu en matière de disponibilité quand beaucoup de nos concurrents étaient victimes de difficultés d’approvisionnement depuis l’Asie, mais nous sommes aussi très concurrentiels au niveau des tarifs. »
C’est aussi l’occasion de voir que même les emballages plastique sont fabriqués par Zéfal ! C’est la première et pas la dernière petite surprise lors de notre visite, tant il est rare de voir des entreprises réaliser autant de choses en interne. « La plasturgie est depuis longtemps un de nos métiers, donc pourquoi sous-traiter ? Par contre, nous avons tendance à réduire de plus en plus la part du plastique dans nos emballage et à préférer de simples supports en carton – qui ne sont pas réalisés en interne mais qui sont tout de même Made in France – dans un objectif de responsabilité environnementale. C’est un domaine dans lequel nous savons que nous devons évoluer, et c’est en cours ».
Un peu plus loin, Franck nous emmène fièrement près de la « machine Bobineau », une des « mamies » de l’entreprise, qui sert à la fabrication de fonds de jantes tressés.
Elle n’était pas en marche lors de notre venue, car la demande ne justifie pas qu’elle tourne à plein régime, mais Franck nous assure que quand on a besoin d’elle, elle démarre toujours au quart de tour.
Changement d’ambiance, avec la partie dédiée à la production de bidons, une des plus importantes activités de Zéfal, pour laquelle on retrouve essentiellement des machines dernier cri. Ce beau bébé peut sortir jusque 400 bidons par heure, avec un procédé d’extrusion/soufflage du polypropylène. Un matériau qui a l’avantage de ne laisser aucune odeur ou goût désagréable au liquide qu’il contient. Une deuxième machine similaire vient d’être acquise pour porter la capacité à 800 bidons/heure.
Plus complexe mais plus qualitative que l’injection, l’extrusion/soufflage se reconnaît à la longue ligne horizontale qu’on trouve en bas des bidons, alors que l’injection, plus adaptée aux très grandes quantités et à une production express, se reconnaît car on trouve plutôt un « point » en bas des contenants, comme sur les bouteilles plastique d’eau minérale ou de soda par exemple.
Une des grandes fiertés de l’entreprise est de pouvoir recycler immédiatement ses déchets dans la chaîne de production. Ainsi, les excès de matière sont directement réinjectés selon un pourcentage précis en même temps que la matière première dans la machine.
Le savoir-faire de Zéfal en matière de bidons, c’est aussi la personnalisation.
Ici aussi, tout est fait en interne, y compris les plaques de sérigraphie, ce qui permet une flexibilité totale. De quelques pièces à plusieurs milliers, tout est possible ou presque.
Lors de l’assemblage final, une opération encore largement manuelle, on constate que ces possibilités de personnalisation séduisent de très prestigieux clients, comme ici un des magasins officiels du Tour de France, qui commande ses bidons chez Zéfal.
Et qui dit bidons, dit bien évidemment porte-bidons ! Ça tombe bien, Zéfal en fabrique aussi, et c’est notamment cela que nous allons découvrir maintenant.
Juste à côté, dans un espace à part, on découvre une nouvelle salle remplie d’autres machines très récentes, pour l’injection d’autres pièces plastique.
Cette fois, on parle de pièces dont le plastique est enrichi à plus ou moins forte dose de fibres de carbone longues pour les doter de propriétés mécaniques particulières. On voit ici bien la différence entre les petites billes de plastique « pur », destinées à la fabrication des bidons, et les petits tubes allongés enrichis de fibres de carbone. Ici, on voit à droite la matière de base la plus haut de gamme, destinée à la fabrication des pièces les plus pointues comme le très léger porte-bidon Pulse L2.
C’est Nicolas Chaumier, à gauche, qui supervise cette partie, particulièrement importante car elle est à la base de bon nombre de pièces du catalogue Zéfal.
En tout, il y a plus de 130 moules différents qui tournent en alternance ! Et devinez quoi ? S’ils ne sont pas fabriqués en interne, ils sont bel et bien entretenus ici grâce à une importante équipe d’entretien et support technique. Et on met un point d’honneur à former la jeunesse, comme ce stagiaire en plein apprentissage (à droite).
Une grande partie des machines est également entretenue en interne grâce à du personnel expérimenté qui se trouve dans l’atelier de mécanique, ce qui limite les temps de mise à l’arrêt.
Tiens, un bruit mécanique assez fort et répétitif parvient à nos oreilles. Qu’est-ce donc ?
Ce n’est autre qu’une impressionnante machine d’assemblage des pompes ! Une des activités historiques de la marque, et qui compte toujours parmi les plus importantes. Savez-vous d’ailleurs que le nom de Zéfal vient de là ? Il s’agit à la base du nom d’un modèle de pompe lancé au milieu des années 1930, venant de la contraction de « Zéfir » (personnification du vent d’ouest) et de « aluminium », le matériau de la pompe, que Zéfal a été un des premiers à utiliser et qui a fait sa renommée. C’est dans les années 90 que ce patronyme s’est imposé à toute l’entreprise.
Revenons à notre fameuse machine : elle date de la fin des années 70, et elle tourne encore chaque jour ! A une époque, elle tournait même en 3x8h. Mais même si cette époque glorieuse est révolue, elle n’est pas près de prendre sa retraite, et elle a même tendance à voir son temps de travail ré-augmenter.
Au niveau des pompes, si tous les modèles sont assemblés en interne, toutes les pièces ne sont pas faites « in house ». Néanmoins, il reste vraiment beaucoup, beaucoup de choses fabriquées ici, comme vous allez le voir. Il y a tout d’abord les corps d’une partie de la famille de pompes.
Non seulement plusieurs corps de pompe sont encore fabriqués ou finalisés ici selon une technique d’emboutissage bien précise…
Mais les joints, ressorts, tuyaux et petits embouts de la plupart des modèles sont aussi faits en interne ! Clairement, nous n’imaginions pas que tant de petites pièces étaient fabriquées ici car elles sont habituellement sous-traitées. Mais l’énorme palette de métiers et de machines dont Zéfal s’est historiquement dotée lui permet cette maîtrise très large de sa production.
Plus que jamais, la tendance est à la relocalisation, comme en témoigne la pompe à pied FP60, 100% Made in France et dont on voit ici le manche en bois du Jura. « C’était le projet de fin d’études d’un de nos anciens stagiaires, nous explique Franck. Il a depuis été engagé dans l’entreprise et nous travaillons à une démarche similaire sur une plus grande part de notre gamme de pompes. »
Actuellement, 30% environ du catalogue Zéfal est produit ailleurs en Europe ou en Asie, et 70% est fait ici, à Jargeau. Comme en témoigne l’impressionnant hall de stockage et les étiquettes d’expédition, l’entreprise reste avant tout un très gros exportateur, dont les produits sont vendus quasiment dans le monde entier.
Avant de nous présenter une petite surprise et d’en finir avec la partie « production », Franck tient à nous montrer les plus anciennes machines de l’entreprise, comme celle-ci qui sert à fabriquer les porte-bidons classiques en fil de métal cintré…
Ou encore une autre qui sert toujours aujourd’hui à fabriquer les fameux cale-pieds Christophe dont nous vous parlions au début de cet article.
Quant à la petite surprise, c’est que Franck a lancé juste avant le début de notre visite, l’impression de garde-boue VTT légers personnalisés à l’effigie de Vojo. Il s’agit d’un des derniers produits ajoutés au catalogue, et pour lequel Zéfal a ajouté encore un nouvel équipement à son parc de machines déjà très fourni, avec cette graveuse/découpeuse laser.
Enfin, avant de partir, impossible de ne pas passer voir Christophe Fletout, sorte de « Géo Trouvetou » de l’entreprise, en charge du développement des produits. On le voit ici dans son bureau, ou plutôt dans son « antre » rempli de prototypes passés, présents et futurs.
C’est aussi lui qui est en charge des tests. « Nous avons des machines assez perfectionnées, comme ce simulateur de roulage que nous avons développé avec Aivee (marque française de moyeux) pour tester nos fonds de jante, nos kits de réparation tubeless et d’autres produits liés aux roues. Mais nous avons aussi des solutions qui peuvent paraître un peu archaïques, mais qui sont en réalité redoutablement efficaces, comme cet ancien cadre attaché au mur et que nous lançons à la main violemment sur le sol de manière répétitive et depuis des hauteurs de plus en plus importantes pour tester par exemple la tenue de notre bagagerie ou de nos porte-bidons, en plus d’une machine à vibrations. Quand nous envoyons nos produits à nos ambassadeurs ou à nos employés cyclistes pour les tests sur le terrain, nous voyons que nous ne nous trompons que rarement avec ce premier essai. »
Christophe est également très fier du développement de la gamme de lubrifiants, produits par des spécialistes du domaine en France et en Allemagne, mais développés, testés et conditionnés ici. « Là aussi, j’ai développé une machine pour automatiser des tests longue durée. Je suis parti d’une ancienne machine de test de pompes qui a été retournée et modifiée. Nous y avons ajouté une injection d’eau et de différents types de particules qui permettent de simuler différentes conditions de roulage. En 24h nous parvenons à simuler des cycles de 400km. Et là aussi, même si la machine n’est peut-être pas la plus « sexy » du monde, cela fonctionne. »
En effet, nous avons pu voir que les huiles Zéfal sont particulièrement performantes lors de notre test que vous pouvez retrouver ici : Test Ride #31 | Huiles, kit mèches et protections de cadre Zéfal.
Voilà, le moment est venu de clôturer cette visite, qui nous a permis de découvrir une entreprise pleine de vie, particulièrement attachante, grâce à des hommes et des femmes attachés à leur métier et au savoir-faire qu’ils détiennent. C’est beau de voir qu’il reste en France de telles entreprises, fières de leur passé et encore pleines d’avenir !