Visite | REIN4CED : passé, présent et futur d’un vélo incassable
Par Yannick Schepers -
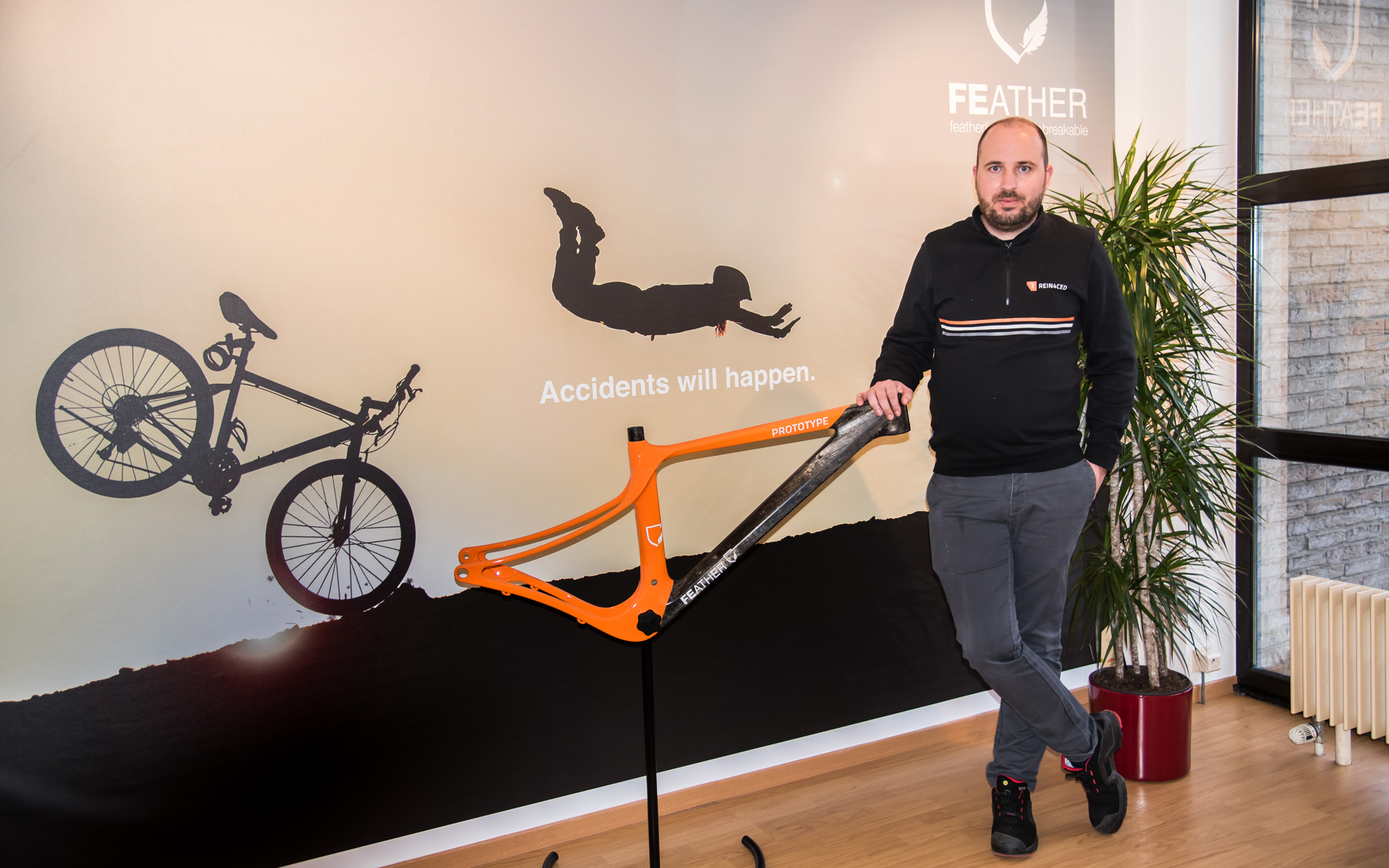
Un mardi après-midi, en janvier. Je gare ma voiture sur le parking d’un complexe d’affaires et je regarde l’horloge. J’ai 15 minutes d’avance, juste assez de temps pour me préparer à ma toute première interview pour Vojo. Dave Luyck, Chief Product Officer de REIN4CED, m’attend. Jamais entendu parler ? L’entreprise n’est née il n’y a même pas 4 ans mais dans sa courte existence, elle a déjà remporté de nombreux prix dans le monde entier. Tout cela grâce à « Feather », le composite avec lequel elle fabrique un cadre de vélo prétendument « incassable », aussi léger que le carbone et aussi résistant que l’acier. Dave va me guider à travers le passé, le présent et l’avenir de la société, avec le bruit de l’usine en arrière-plan en bande sonore de cette conversation. Notre conversation durera une heure et je vais recevoir une véritable leçon sur les dessous de l’industrie du vélo…
Vojo : Dave, comment est née l’idée de lancer REIN4CED ? Dave : REIN4CED a été fondé par trois doctorants de la KU Leuven (l’aile flamande de l’université de Louvain) : Michaël Callens, Niels Degreef et Yannick Meerten. Pendant son doctorat, Michaël a travaillé sur les fibres d’acier. Il a terminé son doctorat et nous utilisons désormais cette fibre d’acier dans nos produits. L’idée de REIN4CED est née du constat qu’il n’existait plus d’industrie manufacturière en Belgique dans le domaine des composites. Cependant, il est frappant de constater qu’il y a beaucoup de connaissances en Flandre avec des autorités internationales comme Joris Degrieck et Ignaas Verpoest qui sont également écoutées à l’étranger. Mais en dehors de la recherche et des publications scientifiques, il s’est passé très peu de choses avec ces connaissances en Belgique. Après le doctorat de Michaël, Niels, qui faisait des recherches sur les nanotechnologies, a lui aussi été stimulé par l’idée de changer cela. C’est ainsi que REIN4CED a vu le jour en 2015. Au départ, il s’agissait d’un cabinet de conseil destiné à soutenir l’industrie dans la recherche en composites. Vojo : À l’époque, il n’était pas encore question de cadres de vélo. Quelles activités ont été menées avec REIN4CED en tant que cabinet de conseil ? Dave : Aider les concepteurs et les ingénieurs, qui étaient auparavant habitués à fabriquer des produits en transposant leurs connaissances de base des métaux aux composites. Dans le monde des composites, on appelle ça du « black metal thinking » et ce n’est pas nécessaire. Nous avons également travaillé sur les applications de la fibre d’acier et les possibilités d’un « composite hybride » fibre d’acier / fibre de carbone. Des recherches ont été menées pour déterminer quelles propriétés pouvaient être créées en mélangeant des fibres de carbone fragiles avec des « fibres d’acier ductiles » (étirables). Vojo : Thomas Edison est passé par 10 000 projets avant d’aboutir à la lampe à incandescence, j’imagine qu’il y avait aussi beaucoup d’expérimentation à REIN4CED dans ces premières années. Dave : Les premiers tests en 2015, bien que très simples, ont immédiatement donné des résultats prometteurs.Par exemple, prenez la fourche en carbone d’un vélo de route et enveloppez-la de fibre d’acier. La rigidité est affectée positivement et vous pouvez taper dessus avec un marteau, elle ne cassera pas. On peut difficilement appeler cela un test académique, mais la preuve que c’était possible était là. Vojo : C’est une façon très spectaculaire de tester l’applicabilité d’un produit. Est-ce la raison pour laquelle REIN4CED s’est lancé dans le marché du vélo ? Dave : Les secteurs de l’automobile et de l’aérospatiale sont en fait les plus gros utilisateurs de matériaux composites. Mais en décembre 2015, Michaël (le CEO) a fait une présentation à Cyclitech, un salon du composite à Bruxelles où l’industrie du vélo était très présente. C’est là qu’est née l’idée que les composites ductiles peuvent avoir des applications intéressantes dans ce domaine. En outre, l’industrie du vélo fonctionne avec une chaîne courte entre le fabricant et le consommateur, ce qui lui permet de travailler facilement avec de nouvelles technologies, de s’y adapter rapidement. Vojo : Etait-ce le tournant pour REIN4CED ? Dave : D’une certaine manière, oui. Après Cyclitech, REIN4CED a commencé à se demander si c’était la direction que l’entreprise devait prendre. À cette époque, je ne faisais pas encore partie de l’entreprise moi-même, mais j’ai été formé comme ingénieur composite et pendant ma jeunesse j’ai aussi couru sur route. Donc, même si ma formation ne concernait vraiment que les applications dans les secteurs automobile et aérospatial, l’industrie du vélo m’a toujours attiré. Avant que REIN4CED ne me demande de m’engager dans ce projet, j’avais déjà des années d’expérience en tant que designer, développeur de cadres et ingénieur chez Eddy Merckx, entre autres. Par conséquent, je connaissais très bien l’industrie du cyclisme. En 2016, j’ai rejoint l’entreprise et la décision de se concentrer sur l’industrie du vélo a été prise. Vojo : En 2016, vous vous êtes donc tournés vers l’industrie du vélo. Comment vous est venue l’idée de prendre également en charge le processus de production des cadres de vélo? Dave : La première raison, c’est que Michaël et Niels voulaient créer des emplois en Belgique avec REIN4CED. Nous aurions en effet pu facilement développer, produire, emballer et envoyer notre matériel en Chine pour qu’il soit livré aux grands fabricants de carbone afin qu’ils puissent produire les cadres de vélo des grandes marques mais cela signifie plus ou moins céder son matériel et vous courez le risque de perdre le contrôle de votre technologie. Nous voulions faire les choses différemment. Je connaissais le processus de production en Chine, qui est manuel et exigeant en main-d’œuvre. Michaël et Niels venaient d’obtenir leur diplôme universitaire et, contrairement à moi, ils étaient très familiers avec les diverses nouvelles technologies et savaient où ils en étaient dans le domaine de la fabrication. Nous sommes arrivés à la conclusion que nous pouvions probablement faire d’une pierre deux coups. Nous pouvions présenter un nouveau type de composite à l’industrie, mais la technologie pourrait aussi être prête pour fabriquer des cadres de vélo en composite de manière automatisée. Vojo : En ce qui concerne les cadres, la Chine affiche les chiffres de production les plus élevés au monde. En quoi ce processus de production diffère-t-il de ce qui se passe chez REIN4CED ? Dave : Tous les cadres actuellement fabriqués en Asie utilisent des thermodurcissables. Vous mettez la matière première dans un moule, qui se réchauffe et durcit. Ce processus n’est pas si facile à automatiser. Nous utilisons du thermoplastique, on chauffe le matériau pour qu’il devienne fluide et flexible et que nous puissions commencer à le façonner. Lorsqu’il refroidit, il prend sa forme solide. La différence avec un thermodurcissable, c’est qu’on peut recommencer encore et encore ce processus.C’est quelque chose de plus intéressant à automatiser. Au moment où nous envisagions cela, la technologie était quasi mature. Ainsi, en 2016, il y avait deux piliers sur lesquels nous avons concentré notre attention. Aurons-nous la technologie nécessaire pour permettre un processus de production automatisé au niveau local ? Et deuxièmement, arriverons-nous à le vendre ? Vojo : A cette époque, REIN4CED était une très jeune entreprise qui devait encore faire ses preuves. Comment vos idées ont-elles été reçues par les grands acteurs de l’industrie du vélo ? Dave : En tant qu’ingénieur en matériaux composites, j’ai toujours été un outsider ; nous ne sommes pas très bien gros dans l’industrie du vélo. Mais malgré cela, je m’étais constitué un large réseau. Je connaissais mes collègues chez d’autres marques de vélo connues. Ainsi, lorsque j’ai dit que nous avions un produit qui pouvait faire ses preuves dans la fabrication de vélos, ils n’ont pas vu en moi le dernier coup marketing, mais ont été intéressés par ce que nous avions à dire.. D’un autre côté, s’il y a une chose dont j’étais sûr, c’est que l’industrie du vélo est un marché conservateur qui ne se laisse pas facilement séduire par les idées nouvelles et les belles promesses. Ce n’est pas comme si on arrivait, qu’on s’asseyait avec les Scott et Trek du monde entier et qu’on repartait à la maison avec une commande de 10 000 cadres. Nous ne savions même pas encore comment passer à la production. Vojo : À l’époque, il y avait encore beaucoup de chemin à parcourir. En tant que petite start-up sans technologie éprouvée, sans usine, vous étiez confronté à un investissement de plusieurs millions. Comment avez-vous géré ça ? Dave : J’ai contacté mon réseau pour obtenir une réponse à l’un de nos deux principaux piliers : « Allons-nous réussir à le vendre ? ». Nous recherchions des acteurs de l’industrie du vélo qui diraient « oui, nous allons suivre cette histoire et nous voulons y associer quelque chose financièrement ». Avec ce bout de papier, nous pouvions montrer aux investisseurs potentiels qu’il y avait un intérêt réel pour le marché. La question suivante à laquelle nous devions répondre était la suivante : « Pouvons-nous tenir nos promesses ? ». Voyez cela dans le sens le plus pratique possible du terme. Est-ce tout simplement faisable ? Entre-temps, nous avons recherché sur le marché européen des technologies, des machines et des moyens de les combiner afin que nous puissions réaliser nos projets. Nous avons réussi. Entre 2016 et 2017, nous avons prouvé un certain nombre de choses, à très petite échelle, et cela s’est traduit par notre première augmentation de capital en 2017. Cela nous a permis de commander les machines, de signer le bail et donc tout s’est accéléré. Vojo : Cette augmentation de capital a-t-elle été réalisée grâce à des aides publiques ? Dave : En partie. À ce moment-là, en 2017, trois parties sont intervenues. Gemma Frisius, le fonds d’investissement de la KU Leuven, Finindus, un fonds d’innovation de l’industrie sidérurgique qui s’engage à soutenir l’industrie manufacturière et Essenscia Innovation Fund, qui est actif dans le domaine de la chimie. Vous pouvez voir et entendre les conséquences de cette injection de capital ici (ndlr : pendant notre conversation, nous pouvons entendre l’usine, qui se trouve derrière le mur de notre salle de réunion mais qui est strictement interdite à tous les non-employés, même le conseil d’administration n’y est pas autorisé). Bien que ce ne soit pas si évident, nous pouvions maintenant démarrer la production et nous devions donc attirer des clients.Nous avions également un autre inconvénient : nous ne voulons pas vendre un processus, nous voulons vendre des cadres de vélo selon un certain processus. Nous avons donc dû chercher ces machines. Nous nous sommes retrouvés chez le fournisseur, qui disposait d’un banc d’essai en Allemagne où nous pouvions effectuer des tests dans cette phase « initiale ». Le fonctionnement de ces machines n’a pas été à la hauteur de nos attentes donc tout ce processus, ces recherches, ont pris du temps. Vojo : Pourquoi cela n’a-t-il pas répondu à vos attentes, que fallait-il changer ? Dave : Je n’oublierai jamais la première fois que nous sommes entrés dans ce hall d’usine. Devant nous, nous voyons l’aile d’un avion privé qui a été développé dans cette usine. Une aile de 7 mètres de long avec une ailette incurvée à l’extrémité. C’est ce que nous voulons faire, avons-nous dit au fournisseur. Nous voulons le même matériau et la même courbe, mais sept fois plus petits que ce que nous voyons ici. Est-ce possible ? Ils n’y avaient pas pensé à l’époque. Ainsi, chaque fois que nous avons demandé si les machines étaient capables de répondre à l’un de nos souhaits, nous avons obtenu invariablement la même réponse : « C’est une question intéressante. On ne sait pas, mais on va essayer« . Cette technologie étant principalement utilisée dans l’aviation, il était nouveau de l’appliquer à quelque chose d’aussi petit qu’un cadre de vélo. Nous avons fini par le tester en utilisant les dimensions d’un cadre que j’avais moi-même conçu il y a longtemps. Si ça marchait, tout marcherait. Cela a fonctionné, mais ce n’était pas encore le bout du tunnel. C’est un processus d’essais et d’erreurs, qui se poursuit encore aujourd’hui. Nous vivons encore des « moments eurêka ».Nous étions déjà en 2018 lorsque nous avons pu dire que nous avions trouvé les bases de la méthode de production que nous utilisons aujourd’hui. Il a fallu attendre jusque mi-2019 pour recevoir les premières machines, puis encore un an et le printemps 2020 avant que tout ne soit là et que nous puissions parler de notre propre chaîne de production. Vojo : 2019 était-elle l’année où REIN4CED a pu se lancer vers une production à plus grande échelle ? Dave : Pour répondre à cette question, je vais vous en dire un peu plus sur notre processus de fabrication. Notre composite est chauffé et transformé en ruban. La machine place automatiquement ces bandes au bon endroit, dans le bon sens et avec le bon empilage, dans le bon angle, sur une plaque. Le tout est chauffé et ensuite pressé. Nous fabriquons une pièce à l’échelle gauche et droite, nous les joignons ensemble et vous obtenez un cadre. Avant cela, nous dépendions d’une tierce partie, un centre de recherche qui nous permettait de travailler sur leurs machines. Les machines n’étaient pas équipées pour cela, donc au début nous avions plus de travail pour produire nos cadres. Depuis avril 2020, nous sommes 100% indépendants des autres, nos machines sont dans notre hall de production et nous avons effectué des tests intensifs pendant toute une année.Nous prévoyons pouvoir commencer à évoluer à partir de mars 2021, car nos processus sont désormais entièrement en place. Entre-temps, nous avons acquis beaucoup de connaissances et nous sommes prêts à prouver ce dont nous sommes capables. Regardez le futur e-bike tout-suspendu de Kellys ou le hardtail qui sera lancé plus tard par Ghost. Nous nous attendons à un grand « coup de boost » lorsqu’ils arriveront sur le marché.
Vojo : Vous évoquez Kellys et Ghost, les marques chez qui nous verront les premiers cadres REIN4CED du marché et, espérons-le, sur les sentiers dès cette année. Comment se fait-il que ces marques « exotiques » soient les premières à choisir REIN4CED?
Dave : C’est peut-être l’inconvénient d’être une entreprise innovatrice et perturbatrice. Parfois, cela joue contre vous. Pour expliquer cela, je dois expliquer comment l’industrie du vélo fonctionne maintenant pour une très grande partie. L’ensemble de l’industrie du vélo a une chaîne d’approvisionnement tournée vers l’Asie. Toutes les pièces sont en Asie : la production des cadres se fait en grande partie en Chine, les composants sont également produits en Asie et plus de la moitié des vélos sont assemblés à Taïwan. De là, il s’agit en fait de « Box Moving », qui consiste à envoyer les vélos finis dans des cartons aux centres de distribution en Europe, qui approvisionnent ensuite les magasins de vélos. La seule chose à faire est de redresser le guidon. À l’exception des montures les plus chères, les vélos les moins chères sont livrés de cette manière, même chez les grandes marques. Plus l’organisation est grande, plus la dépendance à l’égard de la chaîne d’approvisionnement est importante.
C’est pourquoi il n’est pas évident pour nous de lever la main et de faire signe à ces marques pour leur dire « hé, vous pouvez aussi acheter ce cadre en Europe » parce qu’alors vous avez le cadre en Europe mais tout le reste est en Asie.
Vojo : Cependant, il existe aussi de grandes marques qui ont leur siège aux Pays-Bas, par exemple. N’est-ce pas une façon de trouver une solution ?
Dave : Ce sont des sièges sociaux, qui ont un objectif différent. Il n’y a pas de chaîne de production, mais il y a un centre de distribution, par exemple. De la R&D peut également s’y faire, principalement dans le domaine du marketing. Les spécifications auxquelles les vélos en Europe doivent répondre sont examinées à partir de là. Un exemple pour illustrer cela de manière très simpliste est le physique de l’Européen occidental. Nous sommes généralement plus grands que les personnes d’origine asiatique. Cela signifie que nous pouvons avoir besoin du même cadre, mais qu’il doit être équipé de tiges de selle plus longues, de potences plus longues et éventuellement d’autres composants adaptés à notre marché. Ces informations sont ensuite envoyées en Asie pour que les vélos y soient finis selon les spécifications européennes. Alors quand on leur dit que REIN4CED peut également livrer des cadres aux Pays-Bas, ils demandent ce qu’ils doivent en faire (rires).
Vojo : Cela signifie-t-il que vous avez dû chercher des marques qui ne dépendent pas de cette chaîne d’approvisionnement asiatique ?
Dave : Exactement. C’est ainsi que nous nous sommes retrouvés chez Ghost, qui fait partie du groupe Accell aux Pays-Bas. C’est le leader du marché européen des VAE et le deuxième plus grand fabricant de composants de vélos. Ghost utilise Taïwan comme plate-forme logistique pour acheminer ses cadres aux Pays-Bas, où ils sont assemblés avec des composants importés d’Allemagne. Et nous offrons une valeur ajoutée car les cadres représentent toujours un coût élevé dans la production du vélo dans son ensemble et nous pouvons offrir une certaine flexibilité.
Vojo : Qu’entendez-vous par là ?
Dave : Les vélos livrés via Taïwan ont un délai de livraison d’au moins six mois.C’est le temps entre la commande effective et la livraison finale dans l’entrepôt européen.En fait, ils ne passent que 6 semaines dans des conteneurs sur de grands cargos et il ne faut généralement qu’un jour ou deux pour acheminer le vélo de l’entrepôt au magasin.
Comme il y a un délai de plus de 6 mois pendant lequel les marques de vélos ne peuvent plus modifier leur commande, elles doivent commander des vélos à Taïwan sans savoir dans quelle mesure les ventes ont été favorables ou défavorables pendant la période précédente. C’est un facteur limitant majeur. En outre, cela entraîne beaucoup d’incertitude pour les revendeurs, car ils doivent également passer leurs commandes à temps sans pouvoir faire de prévisions concrètes sur les ventes. En Asie, ils travaillent évidemment avec des avances : 30 % du prix d’achat. Cela signifie que vous disposez d’un capital fixe en Asie pendant six mois, en permanence.
Vojo : Et vous ne le faites pas ?
Dave : Nous travaillons différemment. Tout d’abord, nous avons un processus de production automatisé, ce qui nous rend moins dépendants de la main-d’œuvre. Deuxièmement, nous travaillons localement, ce qui nous évite de devoir remplir un conteneur. Nous pouvons facilement faire le plein d’une petite camionnette ou d’un grand camion. Et nous pouvons également livrer toutes les semaines, tous les quinze jours ou tous les mois, selon la demande de la marque. Cela rend la situation intéressante, également en termes de fonds de roulement. Ils passent une commande pour février : un nombre X de cadres dans cette couleur et s’ils ont les groupes en stock à ce moment-là, le vélo sera prêt à être vendu en mars. Le délai de livraison est ainsi réduit à environ 1 mois. Ainsi, le fonds de roulement peut être utilisé beaucoup plus efficacement par les marques.
Cela n’est vraiment possible qu’avec les marques qui ont leurs installations de production ici. Cela nous place en plein dans le « eeshoring » (ramener la production en Europe) avec des marques qui exercent leurs activités ici. Il n’est donc pas surprenant que des marques comme Kellys et Ghost soient les premières à entrer dans cette histoire. C’est une situation gagnant-gagnant.
Vojo : Le marché de REIN4CED n’est-il donc pas trop limité pour se développer réellement vers des applications à grande échelle ?
Dave : Nous pensons que nous sommes prêts au bon moment pour apporter une valeur ajoutée au marché. Les VAE sont en plein essor et l’Europe est le berceau de ce type de vélos. Bosch est le leader du marché des moteurs pour e-bikes ; c’est une entreprise allemande qui fabrique ses produits en Allemagne.
Les VTTAE tout-suspendus sont des vélos chers, à 6000 euros chacun. Trois composants font grimper le prix de revient : le moteur, la batterie et le cadre. Si vous pouvez acheter deux ou même trois de ces composants localement, de sorte que vous n’ayez pas à bloquer le fonds de roulement pendant six mois, il devient possible de faire tourner la production plus rapidement. Puis les marques commencent à calculer et il devient soudain intéressant d’utiliser notre méthode de travail.
Vojo : Aujourd’hui encore, un cadre en aluminium est souvent choisi délibérément dans ce segment des VAE de trail ou d’enduro car le carbone est jugé fragile. Je pense que le marché serait impatient d’utiliser votre composite.
Dave : J’aime t’entendre le dire (rires). Ce n’est pas encore le cas. Nous avons entendu plusieurs raisons à cela, dont la plus courante est « prouvez ce que vous pouvez avant que nous ne fassions des affaires ensemble ».
Mais d’un autre côté, nos amis slovaques de Kellys ont découvert, contre toute attente, qu’il y a beaucoup de gens qui ont ce sentiment au fond de leur tête. La vidéo diffusée sur YouTube pour le lancement de leur vélo d’enduro Kellys Theos a été la plus regardée de tous les temps. Le suivi de ce film autour du matériau utilisé, c’est-à-dire notre composite avec des fibres d’acier, a été gigantesque au niveau international.
Vojo : Vous exploriez le marché pour trouver quelque chose en Europe. Quel a été le facteur convaincant pour Kellys ?
Dave : Il y a deux ans, lorsque nous nous sommes rencontrés avec Kellys, leur point de départ était le suivant : « Nous voulons travailler avec du carbone, mais nous sommes inquiets de l’utiliser sur ce type de vélo ». Comme de nombreux vététistes, ils s’inquiétaient de la fragilité du carbone lorsqu’il est utilisé pour un vélo d’enduro électrique doté d’une lourde batterie de 720 Wh, destiné à être utilisé pour des courses telles que les EWS E-Series. Si quelqu’un emmène ce vélo en montagne, nous voulons être sûrs qu’il rentrera chez lui, et nous ne parlons pas du niveau de la batterie.
Vojo : Les différents composants à partir desquels un vélo est construit jouent un rôle important de nos jours. Par exemple, le choix d’un moteur Bosch ou d’un moteur Shimano peut déterminer le choix final du client. Cela joue-t-il également un rôle pour vous, étant donné que le matériau du cadre est tellement différent de ce qui est actuellement proposé sur le marché ?
Dave : Nous le pensons. Lorsque vous achetiez un vélo de course Merckx et que la chaîne sautait des pignons, c’est le vélo Merckx qui était inutile. Ce n’est plus le cas. Les différents composants sont devenus plus importants aux yeux du consommateur et constituent le plus souvent le facteur décisif dans ce segment des vélos. Si le moteur d’un vélo tombe en panne, c’est Bosch ou Shimano qui sont tenus responsables.
Au niveau du cadre, Kellys n’a pas voulu prendre de risques. Après tout c’est la seule partie qui porte le nom de la marque donc si ça casse, c’est attribué à la qualité et à la fiabilité de la marque. C’est la raison pour laquelle nous sommes entrés en contact avec Kellys et du lancement sur le marché ce printemps des premiers Kellys Theos.
Vojo : J’ai lu sur leur site web que le cadre était incassable. Le carbone, bien que « fragile », présente l’avantage de pouvoir être réparé. Si quelque chose ne va pas avec votre cadre, est-il possible de le sauver ?
Dave : C’est un exemple extrême. Entre « en parfait état » et « en morceaux », il existe heureusement un certain nombre d’étapes intermédiaires. Si on brise un cadre en plusieurs morceaux, il est cassé. Dans le cas des composites, les fibres sont alors tellement endommagées qu’elles ne peuvent être réparées. En définitive, tout est fragile et on ne peut pas tout réparer.
Ce qui nous importe, c’est la fiabilité après l’impact. Et c’est là qu’il est intéressant de comparer les différences entre le carbone et le Feather. Notre composite est constitué de plusieurs couches, dont la dernière est en acier.
Imaginez la situation 1 : vous tombez et votre cadre subit un choc. Dans le cas du carbone, cela provoque une « indentation » dans le matériau. Il est possible que la couche extérieure résiste mais que la couche intérieure se détache et ne soit plus reliée à l’ensemble. À l’extérieur, vous pouvez voir une éraflure, vous ramassez votre vélo et vous dites « ouf, j’ai de la chance, il n’y a rien ». Mais à l’intérieur de votre cadre, il y a certainement des dommages invisibles. Nous appelons cela la délamination. L’intégrité de votre cadre est compromise. Dès qu’une pression trop forte est exercée sur lui à un moment donné, le cadre se brise et c’est irrémédiable.
Aujourd’hui on le voit moins, mais lorsque la première génération de roues en carbone est arrivée sur le marché, c’était différent. Les cyclistes parcouraient de longues distances sur des pavés. On ne voyait rien à l’extérieur mais à l’intérieur de la roue en carbone, il y avait une délamination. Jusqu’au jour où la roue éclate au contact d’un pavé. C’était aussi le résultat d’une délamination invisible pour l’utilisateur.
Mais imaginez la situation 2 : l’impact de la chute est si fort que vous voyez une fissure dans le carbone. Ce type de dommage visible signifie que votre cadre est en fait déjà en deux morceaux, mais qu’il est encore maintenu par le matériau restant. Dans ce cas, vous pouvez réparer le dommage en découpant la fissure et en la remplaçant par une pièce de carbone. Cela permettra de réparer efficacement la fissure et cette partie du cadre pourra même être plus solide qu’aux endroits où la délamination est invisible.
Vojo : Quelle est la différence avec le comportement du Feather face à un impact ?
Dave : Feather est un matériau ductile. Ductile signifie que vous pouvez l’étirer. Par conséquent, ce matériau peut traiter beaucoup plus d’énergie. Cela signifie également que, contrairement au carbone, vous pouvez « cabosser » le Feather. Donc, si vous faites une grosse chute avec un cadre REIN4CED, vous verrez qu’il y a une « bosse » dans le cadre et vous allez penser à la situation 2. Sauf qu’ici, l’acier à l’extérieur du composite ne se brise pas, mais commence à se déformer. Les fibres à l’intérieur du composite ne sont pas brisées et sont toujours connectées les unes aux autres. Alors oui, votre cadre est endommagé, mais vous pouvez toujours rentrer chez vous avec sans aucun problème.
Parlons maintenant de la chute la moins grave : si vous ne voyez pas de bosse, alors il n’y a pas de délamination. Le cadre est exactement dans le même état qu’avant la chute. Il n’y a donc pas lieu de douter des défauts cachés à l’intérieur du cadre. L’acier ayant une « élasticité » beaucoup plus élevée que le carbone, il faut beaucoup plus d’énergie pour le briser en morceaux.
Vojo : Nous parlons ici d’une nouvelle technologie qui doit trouver son chemin vers le consommateur. Les cyclistes sont-ils généralement ouverts à essayer de nouvelles technologies ?
Dave : Je dirais déjà qu’il y a une différence entre les cyclistes et les fabricants pour commencer. Les cyclistes sont très tôt ouverts à l’essai de nouvelles technologies, les fabricants ont besoin de plus de temps pour cela. Il y a ensuite la différence entre la valeur perçue et le fait de mettre effectivement l’argent sur le comptoir. Autrement dit, la différence entre accepter qu’un composant doté de meilleures caractéristiques et d’une nouvelle technologie coûte plus cher et décider qu’il vaut la peine de le payer (rires). Cela reste une considération très personnelle et, en définitive, chacun fait des choix en fonction de sa propre situation.
Vojo : Pouvez-vous déjà faire des prédictions sur les prix autour desquels nous trouverons ce cadre sur différents vélos ?
Dave : Le prix d’un vélo ne dépend bien entendu pas que du cadre. Au final, c’est un exercice que les marques doivent faire elles-mêmes. Kellys utilise une stratégie de prix compétitive. Leur modèle le plus cher, équipé d’une fourche Fox 38 Float Factory, d’un amortisseur RockShox Super Deluxe Ultimate, d’une assistance Shimano EP8 et de notre cadre Feather, sera disponible à un tarif qui tournera autour de 7 500 euros. Dans ce segment de marché, cela ne semble pas être un prix insurmontable.
Vojo : Pouvez-vous nous en dire un peu plus sur les vélos que nous pouvons nous attendre à voir équipés d’un cadre REIN4CED dans un futur proche ?
Dave : Le Kellys Theos devrait arriver sur le marché au printemps. Plus tard cette année, Ghost sortira un hardtail XC haut de gamme utilisant un cadre Feather. Bien sûr, il y a encore des développements passionnants à venir dans les prochaines années, mais pour cela, il va falloir faire preuve d’un peu de patience. Nous vous informerons le moment venu.
Vojo : Nous attendons cela avec impatience.Une dernière question pour conclure : de toute cette aventure, à quel moment vous-êtes vous sentis le plus fier ?
Dave : C’est une très bonne question. Je dois y réfléchir un instant, car nous ne pensons peut-être pas toujours aux étapes que nous franchissons. Un moment dont je suis très fier, dans le volet commercial de mon travail, a été le moment où nous avons pu vendre notre produit pour la première fois. La première fois qu’un client potentiel a choisi de continuer avec notre idée. Quand quelqu’un avec une telle expérience dans l’industrie du vélo veut en faire un projet à long terme, je me suis dit, bon sang, il se passe quelque chose ici.
Lié à cela, il y a eu un moment que je n’oublierai jamais. Cela fait un moment maintenant, mais quand j’y repense, je peux encore facilement revivre le sentiment qui m’a envahi ce jour-là. C’est au moment où nous avons construit un vélo complet pour la première fois. Le moment magique où l’on saisit ce vélo, où l’on s’assied dessus pour la première fois et où l’on parcourt les premiers mètres. C’était ici sur le parking avec le cadre Ghost. J’ai dit à mes collègues : « Vous savez que quelque chose de fondamental a changé à partir de maintenant ? « . Mes collègues ne comprenaient pas ce que je voulais dire et j’ai dit : « À partir de maintenant, nous sommes des constructeurs de cadres ! ». C’est un moment qu’on ne vit qu’une fois.
Plus d’informations : rein4ced.com