Innovations | Bell : bientôt des casques moulés à notre tête ?
Par Léo Kervran -
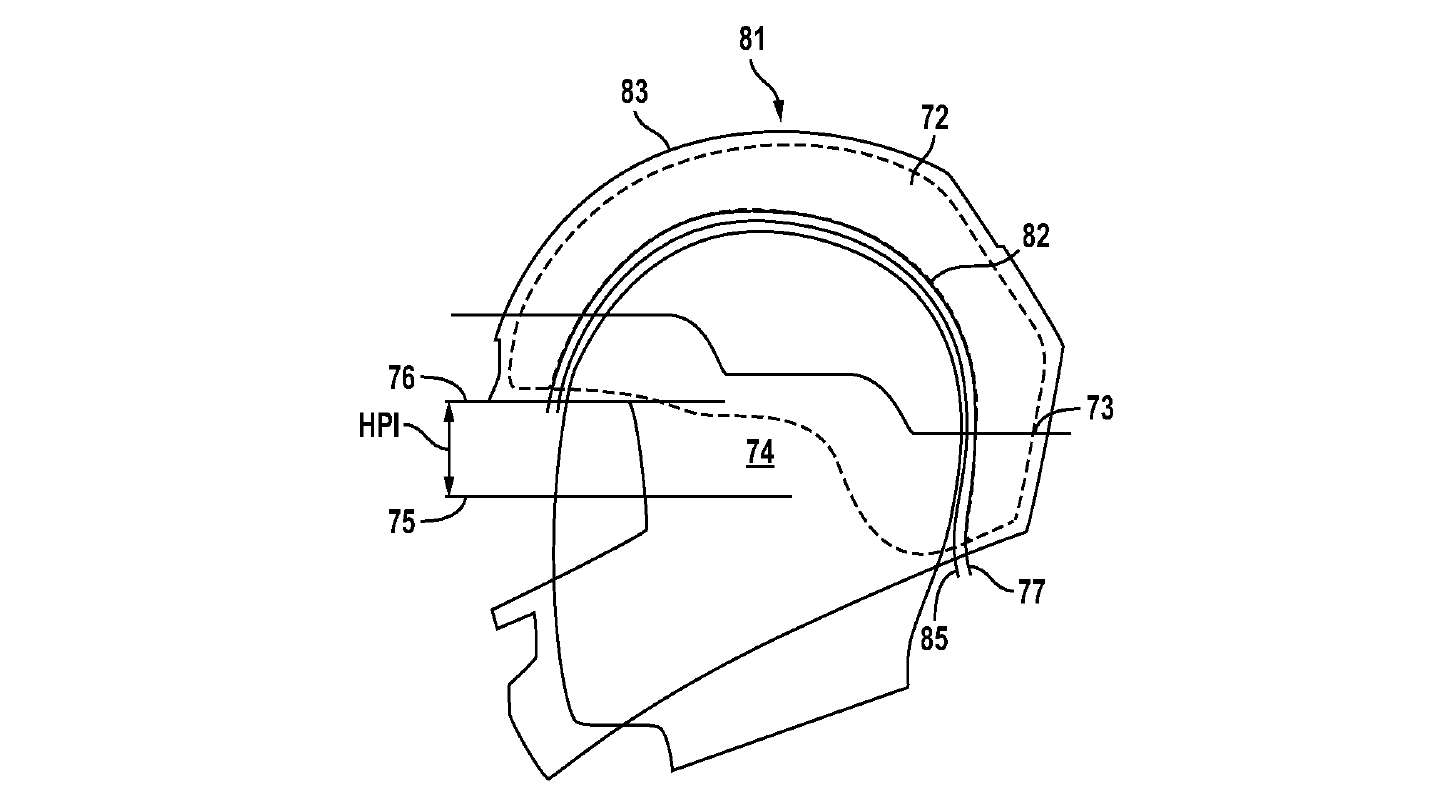
Fondée en 1954 par Roy Richter, la marque américaine Bell est l’un des leaders mondiaux dans le domaine des casques, avec une présence particulièrement marquée dans les mondes du vélo et des sports motorisés. A ce titre, le brevet qu’elle a déposé il y a quelques jours est particulièrement intéressant : elle y décrit des techniques de conception, de fabrication et de test à grande échelle de casques sur mesure…
C’est justement ce qu’explique Bell en introduction du brevet : « la technologie conventionnelle de création de casques a conçu des casques en supposant que les têtes humaines sont similaires et que le tour de tête est le facteur le plus important dans le choix d’un casque approprié. » Nous savons tous que cela n’est pas aussi simple et que la forme de la tête joue un rôle aussi important que sa taille dans le choix du casque. Améliorer le confort d’un casque, c’est réduire les distractions pour le ou la pilote donc améliorer la performance, mais aussi la sécurité, grâce à un ajustement plus précis sur la tête. Or, quoi de plus confortable et ajusté qu’un casque fait sur mesure ?
Pour être tout à fait juste, ce genre de proposition n’est pas exactement nouveau. La petite marque britannique HEXR propose depuis 2019 un casque conçu pour être adapté à la tête de son porteur, mais tant du fait des technologies utilisées (scan de la tête pour créer la modélisation puis impression 3D du casque) que de l’envergure de la marque, cela reste pour l’instant très confidentiel.
Pour être en mesure de proposer une gamme suffisamment variée et économiquement viable, Bell a donc dû réfléchir à d’autres modalités de mesure et de production. Toujours dans la section Contexte, on lit que « les technologies conventionnelles de création de casques ne sont pas pratiques pour créer des casques en forme de tête personnalisés car elles sont chères et les moules sont chers. Il est souhaitable de former un casque sur mesure pour les clients sans avoir besoin d’un équipement coûteux de numérisation et de fabrication, et de créer ce casque sur mesure rapidement et sans nécessiter de moules personnalisés séparés pour chaque casque. »
Le processus commence par la prise de mesures et, dans ce domaine, la marque évoque de nombreuses technologies : « les données de la tête du client peuvent être capturées avec le client présent grâce à l’utilisation d’outils de mesure mécaniques tels qu’une règle, un ruban à mesurer ou des pieds à coulisse, ou à l’aide d’outils optiques tels qu’une photo 2D ou une série de photos ou de vidéos […], par moulage physique de la tête du client, par micromètres laser, sondes tactiles, imagerie par résonance magnétique, tomodensitométrie, balayage des ondes radio, balayage micrométrique de la tête du client ou de parties de la tête du client ». Cependant, c’est bien la prise de photos qui semble avoir sa préférence. C’est d’ailleurs la seule modalité réellement détaillée dans l’article.
Différentes possibilités plus ou moins complexes sont envisagées pour cette prise de photo. Les magasins pourraient être sollicités, en passant par un système de bonnet à poser sur la tête du client. Doté de repères pour faciliter la création d’une image 3D de la tête à partir des photos, ce bonnet permettrait également d’ajuster l’épaisseur du rembourrage du casque selon les préférences du porteur : la face extérieure du bonnet représente la partie en contact avec la coque du casque et tout ce qui est en dessous jusqu’à la face en contact avec le crâne représente le rembourrage. Bell parle ainsi de trois épaisseurs de bonnet différentes (1,5 / 3 / 4,5 mm) ou plusieurs épaisseurs identiques à superposer jusqu’à obtenir le niveau de rembourrage souhaité. 5 photos (vue de face, de gauche, de droite, de derrière et de dessus) suffiraient pour réunir les données nécessaires à la fabrication du casque sur mesure.
Autre possibilité, se passer de bonnet et prendre simplement des photos de la tête, avec un marqueur de taille connue (une pièce de monnaie par exemple) comme référence. Dans ce « mode de réalisation », selon le vocabulaire des brevets, Bell envisage même de développer une application pour guider la personne dans la prise de photo (position de la tête, nombre de photo, qualité suffisante voire contrôle de l’appareil photo d’un smartphone ou d’une tablette).
Notons également que Bell songe à conserver les données physiques de la tête dans une base de donnée, de façon à pouvoir refaire un casque sans prendre de nouvelles mesures. Autre intérêt, pouvoir utiliser ces données pour créer des casques pour d’autres clients au profil similaire : « Il est prévu que bien que des niveaux particuliers plus complets de capture de données soient décrits ici, n’importe lequel des modes de réalisation peut être mis en œuvre avec n’importe quel niveau de détail de capture de données en remplaçant dans les données standard toutes les données manquantes, ou en comparant avec d’autres formes de tête similaires pour personnaliser la topographie de la tête la plus probable pour le client à partir d’autres données client avec des marges acceptables. »
Une fois les mesures prises et la tête recréée en 3D, on passe à la réalisation proprement dite du casque sur mesure. Ici, le brevet décrit deux possibilités : par enlèvement de matière dans la coque en EPS (ou autre matériau), via une machine à commande numérique, ou par addition de matière, avec l’insertion d’une « doublure » sur mesure dans une coque standardisée. Les explications et les détails sur chacun de ces deux modes de réalisation sont relativement précises. On a même droit à quelques indications sur leurs avantages et inconvénients respectifs, mais contrairement aux mesures, Bell ne prend pas vraiment de « parti » (si on peut parler de prendre parti dans un brevet, document purement technique). D’après la marque, les deux méthodes pourraient même être utilisées, suivant le type de casque et la pratique (vélo, sport auto/moto, football américain, hockey…).
Reste un problème, celui des tests normatifs auxquels doivent être confrontés tous les casques mis sur le marché : « Selon les normes d’essai conventionnelles, chaque casque personnalisé devrait être produit en multiples afin qu’un certain nombre de casques ajustés sur mesure puissent subir des tests destructifs pour garantir que la conception d’un seul casque ajusté sur mesure porté par le client satisfait à la sécurité applicable. » On s’en doute, « la production de multiples de chaque casque sur mesure pour les tests destructifs n’est pas une approche commercialement viable pour la production et la vente de casques sur mesure ».
La solution trouvée par Bell est de faire valider ce qu’on pourrait appeler une « unité de base » du casque, c’est-à-dire un produit d’épaisseur inférieure à celle du produit final (le brevet parle de surface certifiée, matérialisée par la ligne 77 ci-dessus). La partie sur mesure serait ensuite creusée dans une épaisseur supplémentaire (continue à la surface certifiée ou dans un autre matériau plus souple) ou ajoutée entre cette surface certifiée et la tête du client selon le mode de réalisation choisi, de façon à s’assurer que le casque respecte quoi qu’il arrive les standards en vigueur.
Une solution qui peut apparaître un peu surprenante compte tenu de la rigueur exigée par les normes, mais vu ce qu’on lit plus loin dans le brevet, il semblerait que ce soit déjà accepté : « le demandeur a travaillé avec les parties responsables de la fondation Snell [spécialiste de la certification des casques] et a établi une méthode de travail acceptable pour positionner de manière cohérente les fausses têtes ISO par rapport aux surfaces certifiées et dans des casques sur mesure, ou des modèles de ceux-ci, dans une manière dont les lignes de test 73 seront constantes ou fixes par rapport à divers casques sur mesure, permettant ainsi à un seul test de certifier la sécurité d’un certain nombre de casques similaires ayant tous des surfaces intérieures différentes, sans le gaspillage de la destruction de casques sur mesure. »
Comme toujours, il faut garder un peu de prudence : publier un brevet n’engage son demandeur à rien et ce document ne signifie en aucun cas que Bell sortira une offre de casque sur mesure d’ici la fin de l’année. Ceci dit, vu le niveau de précision et de détail qu’on a ici, nous avons tout de même beaucoup envie d’y croire… Après le MIPS et les différents systèmes de réduction des accélérations rotationnelles, ce serait une nouvelle grande avancée dans le domaine des casques pour la sécurité et le confort de chacun. Au-delà de ça, cette technologie pourrait même permettre d’améliorer les performances dans certains domaines : en contre-la-montre par exemple, on pourrait optimiser la position du casque par rapport à la tête et au corps du cycliste pour obtenir le meilleur aérodynamisme possible. En VTT, on pourrait imaginer un casque intégral parfaitement conçu pour ne pas du tout interférer avec le champ de vision du pilote. Les possibilités sont nombreuses et nous espérons fortement qu’un tel produit sortira (rapidement, si possible) pour en découvrir plus à ce sujet.
Le brevet complet : System and method for custom forming a protective helmet for a customer’s head