Le nouveau Santa Cruz trial de Danny MacAskill : le carbone du futur ? - A l'intérieur du Carbon Lab de Santa Cruz Bicycles
Par Olivier Béart -
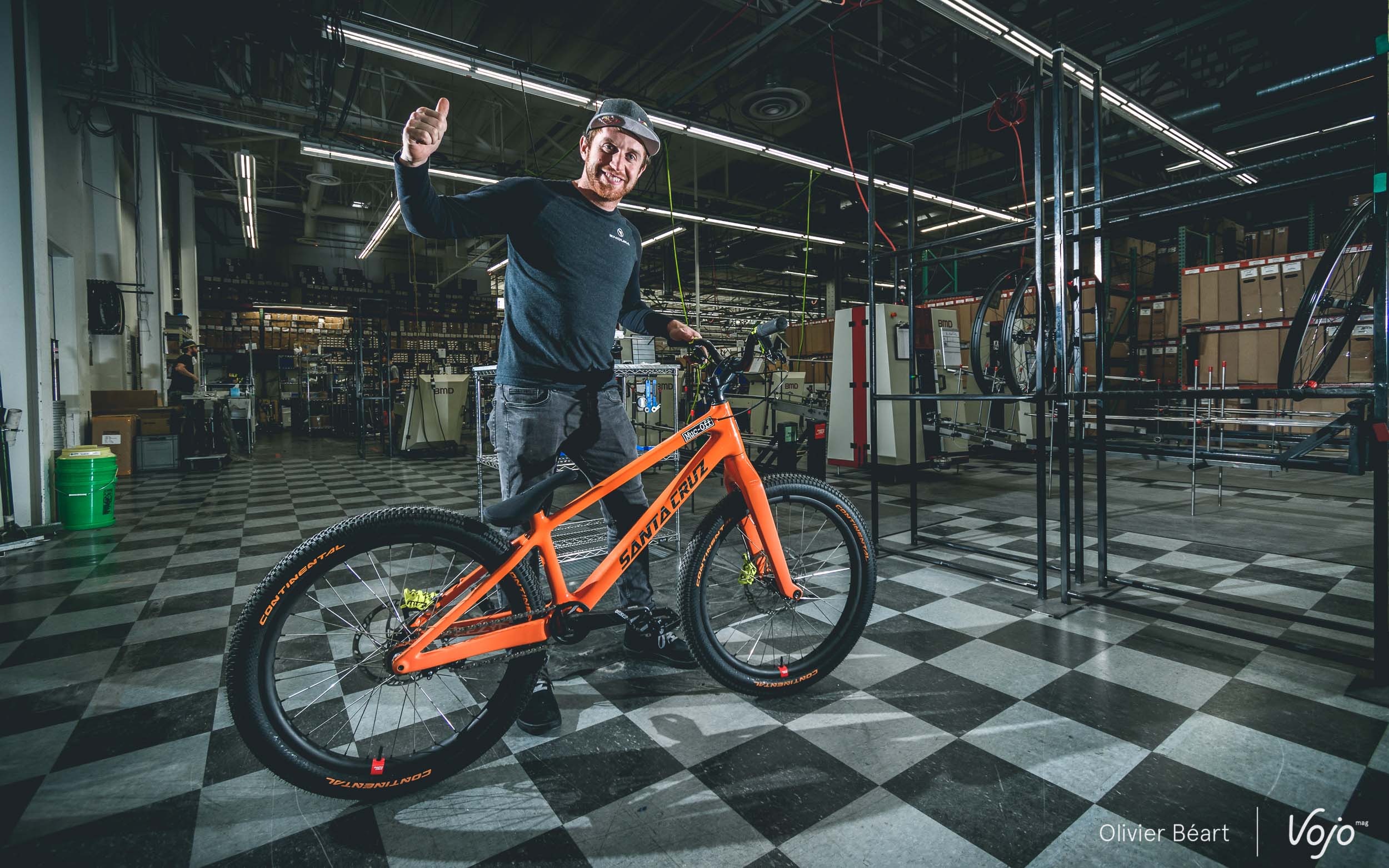
A l’intérieur du « Carbon Lab » de Santa Cruz Bicycles
Pour répondre aux contraintes énormes imposées par la réalisation du nouveau cadre carbone Santa Cruz de Danny MacAskill, les ingénieurs de la marque ont exploré de nouvelles techniques de mise en forme et utilisé de nouveaux types de fibres. Un véritable laboratoire grandeur nature, que nous avons découvert sur place. Suivez le guide !
De dehors, le show-room Santa Cruz Bicycles, situé dans la ville du même nom en Californie, ça ressemble à ça. Mais, quand on a la chance d’être invité dans l’arrière boutique, on découvre d’autres très belles choses. Ca tombe bien, Vojo vous ouvre les portes des zones interdites au public !
Caché tout à l’arrière du bâtiment, derrière la zone d’assemblage des cadres et des vélos complets, juste à côté de la surface dédiée aux roues, se cache une petite salle bien à l’abri des regards : le Carbon Lab. Nicolas McRae, le maître des lieux et ingénieur en chef du département carbone, est intransigeant : pas de photos ! Bon, d’accord, on range notre appareil et on continue la visite avec l’aide des photos officielles, prises par l’excellent Gary Perkin et validées par Santa Cruz afin qu’on ne vous montre pas des choses qui n’auraient pas dû l’être.
Tout d’abord, c’est au niveau des fibres que ce cadre spécialement fabriqué à Santa Cruz pour Danny MacAskill se démarque. En plus des classiques fibres UD ou tressées à 90° qui sont encore utilisées à quelques endroits, un nouveau type de fibres tressées à 60° est également employé. Hyper résistant aux impacts et doté de propriétés très intéressantes pour le VTT, il provient du secteur aéronautique et de la défense. Heureusement que ce cadre est fabriqué « in house » à Santa Cruz car ces fibres fabriquées dans l’Ohio ne peuvent pas sortir des USA, ou alors très difficilement, et en tout cas pas mettre un pied en Chine !
Les fibres, qui arrivent en rouleaux, sont ensuite découpées par cette machine, sorte de cutter à commande numérique. En tout, il y a plus de 500 pièces dans un cadre comme celui de Danny… et chaque forme, ainsi que son placement sur les panneaux pour minimiser les pertes, a dû être calculée et encodée. On vous laisse imaginer le travail.
On passe maintenant à la mise en place dans le moule. Et c’est là qu’on trouve ce qui est sans doute la plus grande originalité dans la construction de ce vélo.
Pour bien comprendre, il faut regarder comment est fabriqué un cadre haut de gamme à l’heure actuelle, comme ici un cadre tout suspendu de la gamme régulière Santa Cruz : les fibres sont enroulées autour de manchons en EPS (sorte de frigolite) qui vont fondre lors de la cuisson, mais qui vont permettre une mise en place précise de toutes les pièces et une excellente compaction des fibres. Ces manchons en EPS sont placés dans des petits « sacs » en plastique qui vont être gonflés une fois le cadre dans le moule pour plaquer les fibres sur les parois.
Cette technique permet déjà de faire des cadres performants et légers, mais lors de la mise sous pression, lorsque le sac se tend et que les petits plis sont censés se défaire, il arrive que des fibres restent coincées ou que des plis persistent. Il faut en tenir compte lors de la conception et prévoir des renforts en conséquence pour ne pas que cela entraîne des soucis.
Ici, Santa Cruz utilise des manchons en latex ! Ceux-ci sont moulés par trempage sur des matrices plastique imprimées en 3D. Un procédé moins coûteux que de faire des matrices en alu CNC et qui permet de réaliser des formes très complexes avec ces espèces de « préservatifs géants ».
Bon, en effet, vous vous en doutez, le latex, c’est tout mou. Les manchons sont donc remplis de billes en plastique, poétiquement nommées « Assballs » par l’équipe du Carbon Lab de Santa Cruz, avant de faire le vide d’air, ce qui leur permet de durcir et d’être enroulés de fibres avant de prendre place dans le moule. « Autre avantage : on peut réutiliser les manchons en latex plusieurs fois, contrairement aux tubes EPS qui sont perdus à chaque utilisation et dont les formes sont aussi moins précises », explique Nicolas McRae, l’ingénieur en charge du Carbon Lab.
« Ensuite, une fois dans le moule, on place le tout dans une presse chauffante et on gonfle les membranes. On exerce une pression de 15t et on chauffe à 150°C. On obtient un niveau de compaction des fibres tout à fait inédit et, au final, une solidité à toute épreuve pour les tubes », ajoute encore fièrement Nicolas.
Le résultat final est effectivement assez sublime au niveau de la finition, tant à l’extérieur… qu’à l’intérieur. Nicolas nous a ensuite mis au défi de casser un des cadres martyrs en le cognant de toutes nos forces sur l’arrête d’un bloc en béton armé qui sert de support à l’une des machines de test du labo. Peine perdue : après plusieurs essais, le cadre est à peine marqué… et le coin du bloc en béton bien effrité !
Reste une dernière opération : l’assemblage des 5 pièces qui composent le cadre final : triangle avant, haubans et bases (gauche/droite). Les pièces s’emboîtent les unes dans les autres et sont fixées assez classiquement à l’aide de bandes de carbone avant une dernière phase de cuisson. La fourche, en une pièce, est aussi construite selon les mêmes procédés que le cadre.
Et voilà, un petit coup de peinture bien voyante (mais qui laisse apparaitre les belles fibres au travers du logo Santa Cruz), et voilà Danny MacAskill prêt à regarder vers ses prochains projets de vidéos !
Photos : Olivier Beart/Vojo & Gary Perkin/Santa Cruz
Pour suivre, faites plus ample connaissance avec le vélo, grâce à ce bikecheck vidéo proposé par Danny MacAskill : www.vojomag.com/video/danny-macaskill-nouveau-santa-cruz
[summary