Coulisses | Chez MET, 3 mois avant le lancement du Parachute MCR
By Christophe Bortels -
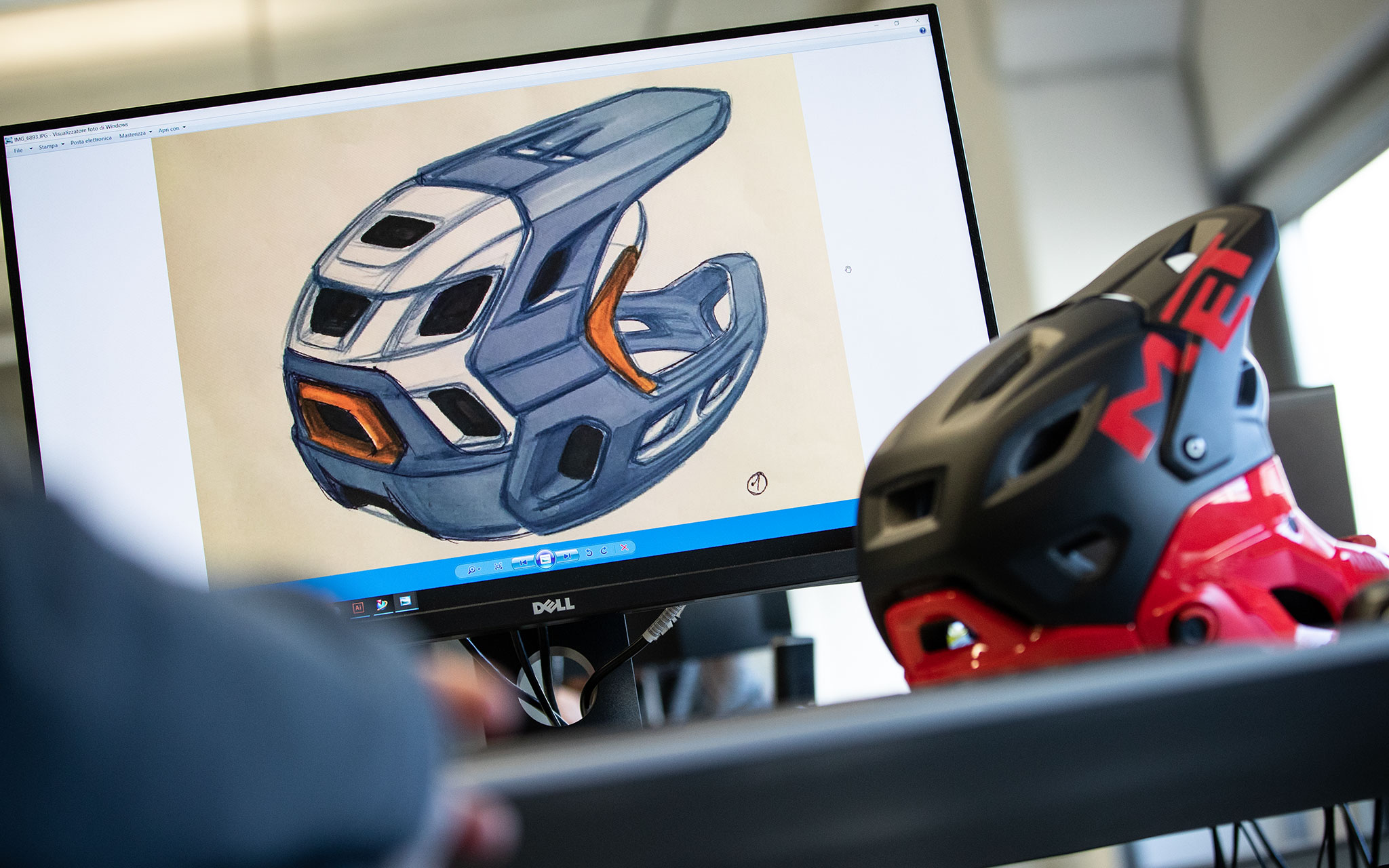
Quelques mois avant la mise sur le marché de son nouveau Parachute MCR, MET nous a ouvert les portes de son quartier général situé à Talamona, tout au nord de l’Italie. Nous avons pu y assister aux derniers tests et préparatifs, mais aussi découvrir comment a été développé ce produit très important dans la gamme du spécialiste italien du casque de vélo. Reportage :
C’est à Talamona, tout près de la ville de Morbegno au nord-est du Lac de Côme, que se trouve le QG de MET, entreprise italienne fondée en 1987 et spécialisée dans la conception et la fabrication de casques pour le VTT et la route.
La façade des bâtiments situés dans une zone industrielle est plutôt discrète et seuls deux oriflammes Bluegrass et MET qui dépassent des grilles indiquent que nous sommes au bon endroit.
Derrière par contre, on découvre une jolie aile de bureaux adossée à la montagne.
Un environnement de travail au plus près de la nature et très lumineux… il y a pire !
MET est une entreprise mondialement connue et l’un des grands noms du casque vélo, que ce soit pour la route ou le VTT, on s’attendait donc à trouver des locaux imposants et des dizaines de personnes.
On découvre avec étonnement des bureaux modernes mais à taille humaine dans lesquels travaillent à peine une vingtaine d’employés, dans une ambiance familiale, le tout toujours chapeauté par le couple de fondateurs, Luciana Sala et Massimo Gaiato.
La production des casques était historiquement réalisée sur place. Mais en 2012, elle a été déplacée en Chine pour une question de réduction de coûts et afin que MET puisse rester compétitif sur un marché très concurrentiel. Deux employés de l’entreprise se trouvent en permanence sur place pour superviser la production délocalisée. A Talamona, quelques moules et autres machines désormais inutilisées témoignent encore du passé industriel des lieux, mais les bâtiments ont pour la plupart été transformés en zones de stockage.
Mais entrons dans le coeur du sujet ! Pour notre visite, MET a aligné dans une salle de réunion des échantillons finalisés du nouveau Parachute. On découvre ainsi en avant-première le nouveau design, les coloris, et on peut même déjà tester le mécanisme de la mentonnière désormais amovible.
Le « papa » du nouveau parachute, c’est lui : Matteo Tenni, 46 ans, ingénieur et Project Manager chez MET, posant ici fièrement avec son nouveau bébé. Il a fallu deux ans pour développer le Parachute MCR, avec un cahier des charges précis, à savoir développer à la fois un vrai casque intégral et un vrai open face. Dans le but de se démarquer sur un marché de l’intégral d’enduro déjà bien fourni, l’idée d’une mentonnière amovible était donc présente dès le début du développement du nouveau Parachute. Et l’intégration d’une solution « magnétique » pour l’interface de la mentonnière également.
Il y a une vingtaine d’années, le processus de conception commençait par des esquisses, ensuite transformées en maquettes faites à la main, elles-mêmes scannées avant de produire les premiers échantillons du casque. Ceux-ci étaient alors soumis à des tests en labo pour voir si les critères de sécurité étaient remplis.
A présent, le développement commence certes toujours par une phase de design, mais les impératifs techniques sont déjà en partie intégrés : Filippo Perini – qui a notamment travaillé chez Lamborghini – a dû en effet en tenir compte tout en imaginant le look en open face et full face. Pour le Parachute MCR, plusieurs mois de travail ont été consacrés au design et quelques dizaines d’esquisses proposées à MET.
Seules quelques-unes de ces esquisses ont passé cette première étape pour ensuite être travaillées en 3D sur ordinateur. A ce stade, il est alors possible de faire des calculs, simuler des impacts et anticiper les résultats du casque aux tests de certification. En fonction de ceux-ci, on peut par exemple rajouter de la matière où c’est nécessaire ou au contraire agrandir des ouvertures pour la ventilation.
Des imprimantes 3D permettent de produire rapidement des versions particulièrement détaillées du futur modèle et de valider un ensemble d’aspects techniques ou de design. Pour des raisons évidentes de sécurité, il n’est par contre pas question de rouler avec, de toute façon avec plus de 3,5kg (!) sur la tête les cervicales ne tiendraient pas bien longtemps… Quatre ou cinq exemplaires du parachute MCR ont ainsi été imprimés. Cette possibilité de produire en 3D en interne a des avantages en termes de confidentialité et permet de gagner un temps considérable dans le processus de développement.
Les trois générations de Parachute côte-à-côte. L’évolution en terme de design est flagrante…
Mais au-delà du design, les coloris sont primordiaux et peuvent déterminer le succès d’un produit. De nombreuses couleurs et combinaisons sont donc testées par le « Art Director » de MET avant d’être soumises à un panel en interne pour être validées, en essayant bien entendu d’anticiper les tendances au maximum.
Le packaging a aussi son importance et, à l’heure actuelle, il fait plus que jamais partie de l’expérience d’achat.
Malgré la présence de Jesse Pinkman et Walter White, nous voici à présent non pas dans un labo de méth, mais bien dans le labo de MET !
Parce qu’un casque est avant toute chose un élément de sécurité primordial dans la pratique du vélo, le labo est l’étape la plus importante du développement d’un produit. C’est ici qu’est mis à l’épreuve tout ce qui a été développé sur ordinateur.
Sous la supervision de Cesare Della Marianna, le spécialiste maison de la torture des casques, MET est capable de reproduire en interne tous les tests de certification – qu’ils soient européens, australiens/néo-zélandais ou américains – par lesquels doivent passer les nouveaux modèles.
Si ces certifications sont obligatoires avant toute mise sur le marché, la norme ASTM F1952 ne l’est pas, mais les fabricants y accordent une grande importance – et en font un argument de vente – puisqu’elle régit les casques destinés à la descente et pousse donc les exigences plus loin encore.
C’est notamment le cas en ce qui concerne la mentonnière qui, sous un certain type d’impact frontal, ne peut se déformer que de maximum 60mm. MET de son côté a estimé que le bon compromis se situe à 30mm de déformation. Et c’est exactement la valeur que l’on retrouve dans la partie témoin (en vert à gauche), marquée par une pointe fixée au poids lors du test effectué devant nous pour mesurer ladite déformation. On remarquera aussi que la mentonnière est transparente, ce qui permet de voir l’état de sa structure après impact.
Au fil des mois, ce sont ainsi plusieurs centaines d’échantillons qui prennent des coups en laboratoire et sont sacrifiés pour la sécurité de l’utilisateur… Une fois que tout est validé, une série d’exemplaires de pré-production sont fabriqués afin de vérifier si la qualité de fabrication (finition, etc) est constante et si la production définitive peut être lancée.
Après un lunch pizza/café dans la cantine de l’entreprise, notre visite se termine. Merci à MET de nous avoir ouvert ses portes ! La présentation et le test du Parachute MCR sont à retrouver dans notre article.